Pioneer hydraulic couplers are a cornerstone of modern agricultural and industrial machinery, enabling the quick and efficient connection and disconnection of hydraulic lines. Understanding the different types, features, and standards associated with these essential components is vital for anyone involved in procurement, maintenance, or operation, like Mark Thompson, a company owner sourcing materials globally. This article dives deep into the world of Pioneer style hydraulic couplers, exploring everything from basic function and design variations (like poppet vs. ball valves) to ISO compliance, key purchasing considerations, and proper usage, ensuring you have the knowledge to select the right product for your needs and maintain operational efficiency. Reading this will help you navigate the complexities of sourcing these critical parts, ensuring quality and compatibility for your equipment.
What Are Pioneer Hydraulic Couplers and Why Are They Essential?
At its core, a hydraulic coupler is a specialized connector designed to join hydraulic hoses or lines together, allowing fluid power to be transmitted between different parts of a machine or between a machine (like a tractor) and its attachments. The "Pioneer" name refers to a specific, widely adopted style of hydraulic coupler, originally developed by the Pioneer company (now part of Parker Hannifin) but now also manufactured by various other companies adhering to the same design principles. These are often called "Pioneer style" couplers. Their primary advantage lies in their ability to facilitate quick connections and disconnections without the need for tools and with minimal fluid loss.
Imagine a farmer needing to switch between different implements on their tractor – a plow, a bailer, a loader. Each requires hydraulic power. Without quick couplers, this process would involve manually unthreading and tightening fittings, leading to significant downtime, potential spills, and contamination risk. Pioneer hydraulic couplers streamline this workflow dramatically. The male half (plug) on the implement hose pushes into the female half (socket or body) on the tractor, locking securely in place with an internal valve mechanism (either poppet or ball) automatically opening to allow hydraulic fluid flow. Disconnecting is just as easy, typically involving retracting a sleeve on the female coupler, which simultaneously closes the valves in both halves before separation, minimizing spills.
This efficiency is crucial in demanding environments like agricultural settings and construction sites. The ability to rapidly connect and disconnect attachments increases productivity, reduces labor costs, and enhances safety by minimizing exposure to hydraulic fluid. Therefore, understanding the function and benefits of Pioneer hydraulic couplers is fundamental for anyone managing or operating heavy machinery. They are not just connectors; they are productivity enhancers.
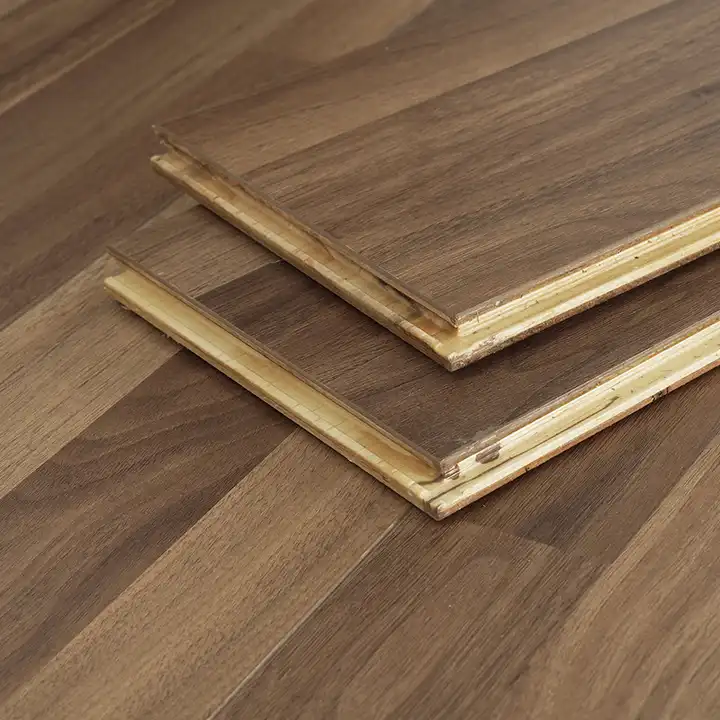
Understanding Different Pioneer Hydraulic Coupler Styles: Poppet vs. Ball Valve
While "Pioneer style" generally refers to the dimensional and functional standard (especially interchangeability under ISO 5675), there are two primary internal valve mechanisms used within these hydraulic couplers: the poppet valve and the ball valve. Choosing between them depends on the specific application requirements, particularly regarding flow characteristics, sealing reliability, and tolerance to contamination. Both types aim to provide a secure connection and minimize leakage upon disconnect.
The poppet valve design is perhaps the most traditional and widely recognized in Pioneer hydraulic couplers. It uses a spring-loaded, mushroom-shaped poppet that seals against a seat inside the coupler body. When the male plug is inserted, it pushes the poppets in both the male and female halves off their seats, allowing hydraulic fluid to flow. Upon disconnection, the springs force the poppets back onto their seats, sealing the lines. Poppet valve couplers are generally robust and offer good sealing under pressure. However, they can sometimes be more restrictive to flow compared to ball valves, and the sealing surface can potentially trap debris, which might compromise the seal over time if not kept clean. The poppet valve mechanism is common in many agricultural applications.
The ball valve design, on the other hand, uses spherical balls pushed against a seat by springs or hydraulic pressure to create a seal. When connected, the mating male tip mechanically pushes the balls off their seats. Ball valve couplers are often favored for their potentially higher flow rates (higher GPM) and lower pressure drop compared to poppet designs of the same size. They are also sometimes considered to have a slight advantage in certain high-pressure or impulse applications. However, some designs might be perceived as slightly more susceptible to contamination affecting the sealing surfaces. Both poppet and ball valve Pioneer style couplers are designed to meet the basic requirements of quick connection and disconnection, but understanding these internal differences helps in selecting the best product for performance and longevity in your specific hydraulic system.
Comparison Table: Poppet vs. Ball Valve Pioneer Style Couplers
Feature | Poppet Valve Coupler | Ball Valve Coupler |
---|---|---|
Mechanism | Spring-loaded mushroom-shaped poppet | Spring/pressure-loaded spherical balls |
Flow Rate | Generally good, can be slightly lower | Often higher flow (higher GPM) |
Pressure Drop | Can be slightly higher | Often lower |
Sealing | Robust, good under pressure | Effective, potentially better in impulses |
Contamination | Can trap debris on seat | Sealing surfaces can be sensitive |
Common Use | Very common in agricultural standard | Preferred for higher flow applications |
Pioneer Type | Both are available in Pioneer style | Both are available in Pioneer style |
Are Pioneer Couplers ISO 5675 Compliant? Decoding the Standard
A common question, especially for procurement officers like Mark Thompson sourcing internationally, is whether Pioneer hydraulic couplers comply with recognized standards, particularly ISO 5675. The ISO 5675 series standard specifically applies to agricultural tractors and machinery, defining the dimensions and requirements for hydraulic couplers to ensure interchangeability between different manufacturers' products. This is crucial for ensuring that a male plug from one brand can correctly connect and function with a female body from another brand, provided they both adhere to the standard.
Generally, the classic Pioneer style hydraulic coupler (both poppet and ball types) is designed to meet the requirements of the ISO 5675 series. This standard dictates the critical dimensions of the male tip and the female body, the locking mechanism engagement, and performance criteria like pressure ratings and allowable leakage. When a supplier states their Pioneer style coupler is ISO 5675 compliant, it implies that their product should successfully interchange with other ISO 5675 compliant couplers of the same size (e.g., 1/2" body size). This provides users with flexibility and avoids vendor lock-in.
However, it's crucial to verify this compliance for any specific product you intend to purchase. Reputable manufacturers will explicitly state ISO 5675 compliance in their product specifications or certifications. Be cautious with unbranded or suspiciously low-price couplers, as they might not fully meet the standard's tolerances or performance requirements, potentially leading to connection issues, leakage, or premature failure. Always request documentation or confirmation of ISO 5675 compliance, especially when sourcing hydraulic couplers for critical agricultural or construction applications where reliability and interchangeability are paramount. This ensures the coupler you buy will integrate seamlessly with existing equipment.
What Key Features Define a High-Quality Hydraulic Coupler?
When selecting a Pioneer hydraulic coupler, several key features distinguish a high-quality, reliable product from a subpar one. Paying attention to these details ensures longevity, safety, and optimal performance of your hydraulic system. First and foremost is the material construction. High-quality couplers are typically machined from high-grade steel, often treated (e.g., carbonitriding or zinc plating) for corrosion resistance and durability, especially important in harsh agricultural or outdoor environments. The internal valve components (poppet or ball) should also be made from hardened steel for wear resistance.
The sealing mechanism is critical. Look for couplers with high-quality seals (often Nitrile/Buna-N as standard, with options like Viton for higher temperatures or specific fluids) designed to provide a leak-free connection under pressure and minimize spillage during disconnect. The design of the valve (poppet valve or ball) and its seat affects sealing performance and flow characteristics (GPM). A reliable locking mechanism, often involving locking balls engaging a groove on the male plug, is essential to prevent accidental disconnection under pressure or vibration. Many Pioneer style couplers feature a double-acting sleeve – meaning you can push or pull the sleeve to connect or disconnect, offering flexibility.
Other important features include the rated working pressure (ensure it meets or exceeds your system requirements), the rated flow (GPM capacity), and the ease of connection (especially connecting under residual pressure, though connecting under system pressure is generally not recommended or possible). High-quality couplers often incorporate design elements that facilitate easier push-to-connect action. Dust caps or plugs are also a vital accessory, protecting the coupler ends from contamination when disconnected – dirt is a major enemy of hydraulic systems and coupler longevity. Considering these features helps ensure you purchase a durable and reliable Pioneer hydraulic coupler.
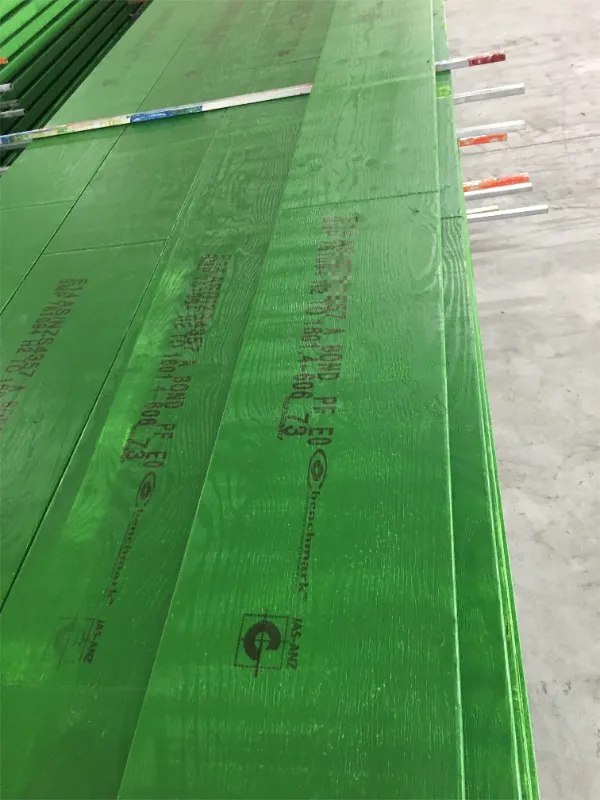
How Does the Pioneer Brand (Style) Compare in the Hydraulic Coupler Market?
The "Pioneer" name carries significant weight in the hydraulic coupler market, particularly within the agricultural sector. Originally an independent company, Pioneer established the dominant style of quick coupler used on North American tractors for decades. Parker Hannifin later acquired the Pioneer brand, continuing its legacy. When people refer to "Pioneer couplers," they often mean this specific, widely interchangeable ISO 5675 style, whether it's an original Parker-Pioneer product or a compatible coupler from another manufacturer.
Compared to other hydraulic coupler types (like flat-face or screw-to-connect), the Pioneer style offers a good balance of performance, reliability, and price, especially for moderate pressure agricultural and general industrial applications. Its key strength lies in its ubiquity and interchangeability (ISO 5675). This means users can often mix and match male plugs and female bodies from different reputable suppliers, offering flexibility in sourcing and replacement parts. The brand reputation (both the original Pioneer and the current Parker-Pioneer) is generally associated with quality and reliability, built over years of field use.
However, numerous companies now manufacture Pioneer style hydraulic couplers. While this offers competitive pricing and availability, it also means quality can vary. Premium brands like Parker-Pioneer, Eaton (Aeroquip), Dixon, and Stucchi often command a higher price but are known for stringent quality control, durable materials (steel construction), and consistent performance. Lower-price alternatives, often sourced online or from less established suppliers, might meet the basic dimensional requirements for interchangeability but could potentially compromise on material quality, seal life, valve performance (poppet or ball), or overall durability. For critical applications, sticking with reputable brands known for quality and adherence to standards like ISO 5675 is often the best long-term investment, even if the initial price is higher. Mark Thompson, valuing quality alongside price, would weigh this trade-off carefully.
What Factors Influence Pioneer Hydraulic Coupler Price?
The price of a Pioneer hydraulic coupler can vary significantly based on several factors. Understanding these can help buyers like Mark Thompson make cost-effective decisions without sacrificing necessary quality. One primary factor is the brand. Original Parker-Pioneer products or those from other major international brands typically command a premium price due to established reputations, quality control processes, and often, more robust materials and engineering. Generic or lesser-known brands, particularly those manufactured in regions with lower production costs, can offer substantially lower prices, but require careful vetting regarding quality and compliance (ISO standards).
The type and size of the coupler also heavily influence the price. Ball valve couplers might sometimes be priced differently than poppet valve couplers of the same size, depending on the manufacturer and specific design. The body size is a major determinant – larger couplers (e.g., 3/4" or 1") naturally cost more than smaller ones (e.g., 1/4" or 1/2") due to the increased amount of material (steel) and manufacturing complexity. Specific features like enhanced corrosion resistance, higher pressure ratings, special seal materials (e.g., Viton vs. standard Nitrile), or designs allowing connection under residual pressure can also add to the cost.
Other factors include order volume (bulk purchases usually attract lower per-unit prices), supplier margins (distributor vs. direct from factory), and logistics costs, especially when sourcing internationally from countries like China. Certifications play a role too; a coupler explicitly certified to ISO 5675 or other relevant standards might carry a slightly higher price reflecting the testing and compliance costs. When comparing prices, it's crucial to ensure you're comparing apples to apples – same size, type (poppet/ball), material specification, brand tier, and compliance level – to accurately assess value. Finding a supplier who offers a good balance of competitive price and reliable quality, like sourcing high-quality building materials directly from a factory, can lead to significant savings.
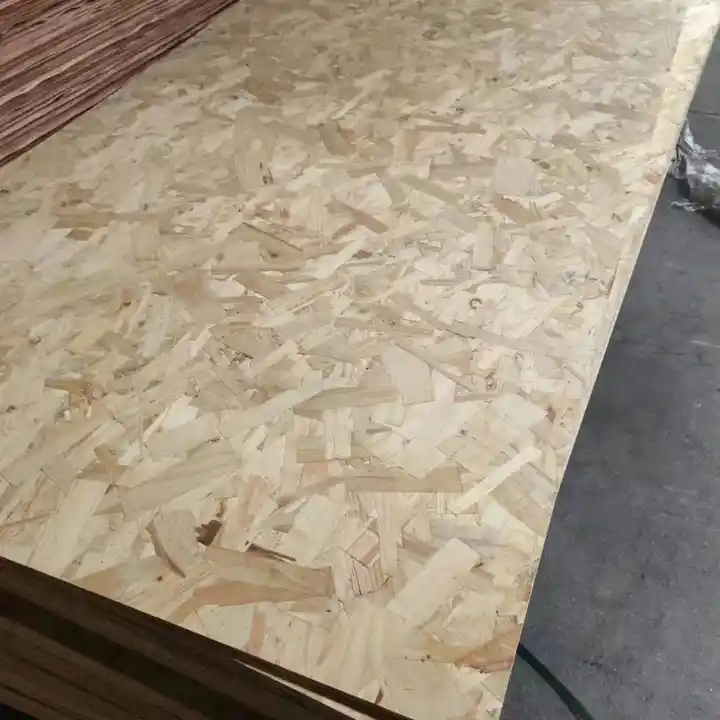
Choosing the Right Pioneer Product: Male vs. Female Couplers Explained
Understanding the difference between male and female hydraulic couplers is fundamental, yet crucial for ensuring you order the correct part. A complete hydraulic quick connection always requires one male component and one female component designed to mate together. In the context of Pioneer style couplers, these are often referred to as the plug (male) and the socket or body (female).
The male coupler, or plug, is typically characterized by its protruding tip which houses part of the internal valve mechanism (poppet or ball). This tip is inserted into the female coupler. The male part usually features a groove around its circumference where the locking balls from the female part engage to secure the connection. Male couplers are commonly found on the hoses of hydraulic attachments or implements (like loaders, backhoes, or agricultural tools).
The female coupler, also known as the socket or body, is the receptacle for the male plug. It contains the other half of the valve mechanism and the locking system (usually locking balls held in place by a retractable sleeve). The sleeve is typically pulled back (or sometimes pushed, in double-acting designs) to allow the male plug to be inserted or removed. Female couplers are most often mounted directly onto the machine, such as the hydraulic outlets on a tractor or excavator, or sometimes on fixed hydraulic power units. When ordering Pioneer hydraulic couplers, it's essential to specify whether you need the male plug, the female body, or a complete couple (set). Ordering the wrong part means you won't be able to make the required connection. Always check the existing fittings on your tractor and attachment to confirm which type you need to replace or add.
Tips for Safely Connecting and Disconnecting Pioneer Hydraulic Couplers
While Pioneer hydraulic couplers are designed for quick and easy operation, following proper procedures for connection and disconnection is vital for safety and preventing damage to the coupler and hydraulic system. Improper handling can lead to fluid injection injuries (which are extremely serious), component damage, and contamination.
Before Connecting:
- Cleanliness is Key: Thoroughly wipe both the male plug and the female coupler body with a clean, lint-free rag. Pay special attention to the mating surfaces and internal areas. Dirt or debris can damage seals, cause leakage, and contaminate the entire hydraulic system. Using protective dust caps and plugs when couplers are disconnected is the best practice.
- Relieve Pressure: Whenever possible, relieve any trapped hydraulic pressure in the lines before attempting to connect or disconnect. Trying to connect against high pressure can be difficult or impossible and can damage the coupler valves (poppet or ball). Some coupler designs tolerate connection under low residual pressure, but system pressure should always be relieved.
- Alignment: Align the male plug squarely with the female coupler body.
Connecting:
- Retract Sleeve (if needed): On many Pioneer style couplers, you may need to retract the sleeve on the female body first.
- Insert Firmly: Push the male plug firmly into the female coupler until it clicks or seats fully. You should feel the locking mechanism engage.
- Check Connection: Gently tug on the hose or fitting to ensure the connection is secure and the coupler halves won't separate. Ensure the sleeve (if applicable) has returned to its forward (locked) position.
Disconnecting:
- Relieve Pressure: Again, relieve hydraulic pressure in the lines first if possible.
- Retract Sleeve: Firmly grasp the hose or fitting and retract the sleeve on the female coupler body.
- Pull Apart: Pull the male plug straight out of the female coupler. Do not twist or angle excessively.
- Cap Ends: Immediately place dust caps and plugs on the disconnected coupler ends to prevent contamination.
Following these simple steps ensures a safe, leak-free connection and extends the life of your Pioneer hydraulic couplers.
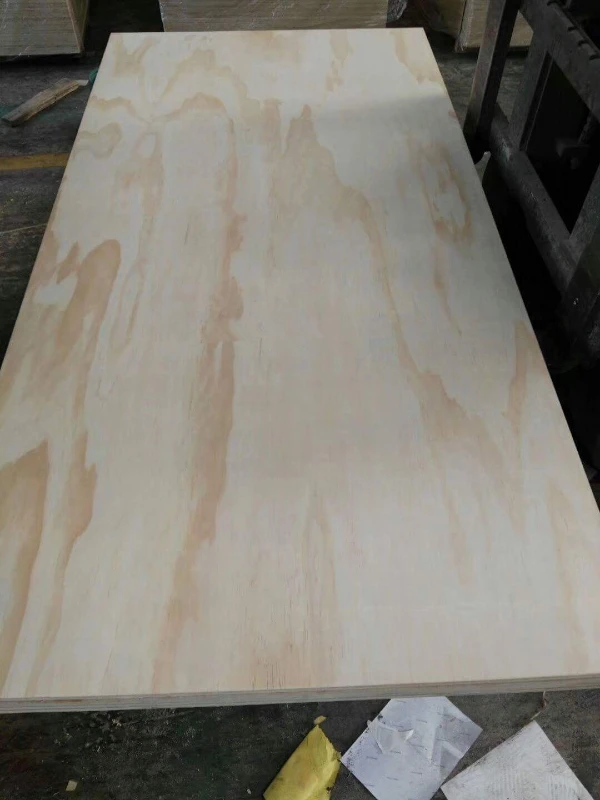
Common Applications: Where Are Pioneer Style Couplers Predominantly Used?
Pioneer style hydraulic couplers are extremely prevalent across a range of industries, but their stronghold is undoubtedly in the agricultural sector. For decades, they have been the de facto standard for connecting hydraulic implements to tractors in North America and many other regions adhering to ISO 5675. You'll find them on virtually every type of tractor attachment imaginable: front-end loaders, backhoes, mowers, tillers, planters, balers, hydraulic top links, and remote hydraulic circuits. Their robust design, ease of use, and established interchangeability make them ideal for the demanding and varied tasks involved in farming. The familiar poppet valve Pioneer coupler is a common sight on John Deere, Case IH, New Holland, and many other tractor brands.
Beyond traditional farming, these couplers also find significant use in related industries. Lawn and garden equipment, compact tractors, skid steer loaders, and some smaller construction machines often utilize Pioneer style couplers for auxiliary hydraulic functions, such as powering grapples, augers, or breakers. Their relatively simple design and cost-effectiveness make them suitable for these applications where ultra-high pressures or zero-spill requirements (better met by flat-face couplers) are not the primary concern.
While less common in heavy construction equipment (which often favors flat-face or specific proprietary couplers), Pioneer style couplers might still be used for certain auxiliary circuits or older machinery. They can also be found in some industrial settings for connecting hydraulic tools or mobile equipment. Essentially, anywhere a quick, reliable, and cost-effective hydraulic connection is needed for moderate pressure applications, particularly where interchangeability with existing agricultural or general-purpose equipment is desired, the Pioneer style hydraulic coupler remains a popular choice. This wide range of use highlights the enduring utility of this classic quick connect design. Companies involved in supplying materials for these sectors, like providers of structural LVL timber for building frameworks or durable formply for concrete work, often interact with clients who rely heavily on equipment fitted with these couplers.
Maintaining Your Hydraulic Couplers for Longevity and Optimal Performance
Proper maintenance is key to ensuring your Pioneer hydraulic couplers function reliably, provide a leak-free seal, and achieve their maximum service life. Neglecting maintenance can lead to frustrating connection difficulties, dangerous high-pressure leaks, system contamination, and costly downtime. Fortunately, basic coupler care is straightforward and highly effective.
The single most important maintenance task is keeping the couplers clean. As mentioned before, dirt, dust, grit, and moisture are the enemies of hydraulic systems and connectors. Always use clean dust caps on the female body and plugs on the male ends whenever the couplers are disconnected. Before making a connection, meticulously wipe both mating halves clean. Inspect the sealing areas inside the female coupler and on the male tip for any embedded debris or damage. Even small particles can compromise the poppet or ball valve seal, leading to slow leaks or weeping.
Regularly inspect the couplers for signs of wear or damage. Check the male tips for nicks, burrs, or deformation. Examine the female body for cracks, excessive wear in the bore, or damage to the sleeve or locking mechanism. Inspect the internal seals (if visible) for cuts, tears, or swelling. A damaged coupler part should be replaced promptly. Also, check the connection security – if a couple feels loose or wobbles excessively when connected, the locking mechanism or mating surfaces may be worn. Trying to force a connection with damaged or excessively worn couplers can lead to further damage or unsafe operation. Replacing a worn non-structural plywood sheet might be straightforward, but a failing hydraulic coupler under pressure is a serious hazard. Consistent maintenance ensures safe and efficient operation, much like using quality materials in any project.
Finally, consider the hydraulic fluid itself. Using the correct type of fluid and keeping it clean through proper filtration is crucial for the entire system, including the couplers. Contaminated fluid accelerates wear on valve components (poppet/ball) and seals. Adhering to the machinery manufacturer's recommendations for fluid type and change intervals will contribute significantly to the longevity of your Pioneer hydraulic couplers and the overall health of your equipment.
Key Takeaways: Pioneer Hydraulic Couplers
- Definition: Pioneer hydraulic couplers are a widely used style of quick connect fitting, primarily in agricultural machinery, allowing tool-free connection/disconnect of hydraulic lines.
- Types: The main internal mechanisms are poppet valve and ball valve, differing slightly in flow characteristics and contamination tolerance.
- Standard: Most Pioneer style couplers are designed to comply with ISO 5675, ensuring interchangeability between compatible brands and products. Always verify compliance.
- Components: A connection requires a male (plug) and female (body/socket) coupler. Ensure you order the correct part.
- Quality Features: Look for robust steel construction, reliable seals, secure locking mechanisms, appropriate pressure/flow ratings (GPM), and ease of use. Consider the brand reputation versus price.
- Safety & Use: Always clean couplers before connection, relieve pressure when possible, ensure a secure lock, and use dust caps/plugs when disconnected.
- Applications: Predominantly used on tractors and agricultural implements, but also found on some construction and industrial equipment.
- Maintenance: Regular cleaning, inspection for wear/damage, and using clean hydraulic fluid are essential for a long, leak-free service life.
By understanding these aspects of Pioneer hydraulic couplers, users and procurement specialists can make informed decisions, ensuring efficient operation, compatibility, and safety in their hydraulic systems.
Post time: Apr-24-2025