Plywood. It's a term you hear constantly in construction, furniture making, and even DIY projects. But what makes this engineered wood panel so special? Often working behind the scenes, plywood is truly the backbone of modern construction and design. This article delves into the world of plywood, exploring its manufacturing, types, applications, and why selecting high-quality plywood is crucial for the success and longevity of any project. Whether you're a large-scale construction company owner like Mark Thompson, sourcing materials globally, or a weekend DIY warrior, understanding plywood is key. We'll cover everything from structural plywood essentials to choosing the perfect plywood for your specific needs, ensuring you make informed decisions for durable, reliable results.
What Exactly is Plywood and Why is it a Construction Staple?
At its core, plywood is an engineered wood product. Unlike solid wood, which is milled directly from logs, plywood is manufactured by layering thin layers of wood veneer together. These layers, often called plies, are glued under heat and pressure. A crucial detail in the manufacturing process is that the grain direction of each adjacent layer is typically rotated by 90 degrees. This cross-graining technique is the secret behind plywood's remarkable strength and stability. It distributes strength evenly across the panel, significantly reducing the chance of splitting when nailed at the edges and minimizing expansion and shrinkage compared to solid wood.
The inherent properties derived from this construction make plywood incredibly valuable in building. Its impressive strength-to-weight ratio, dimensional stability, and resistance to cracking, bending, and warping make it a preferred choice for a vast range of applications. From forming the sturdy skeletons of buildings (floors, walls, roofs) to crafting fine furniture and cabinetry, plywood provides a reliable and workable material. Its versatility allows it to be used in both structural applications where load-bearing capacity is critical, and in decorative applications where aesthetic appeal and a smooth finish matter. This blend of durability and adaptability firmly establishes plywood as a cornerstone of modern construction.
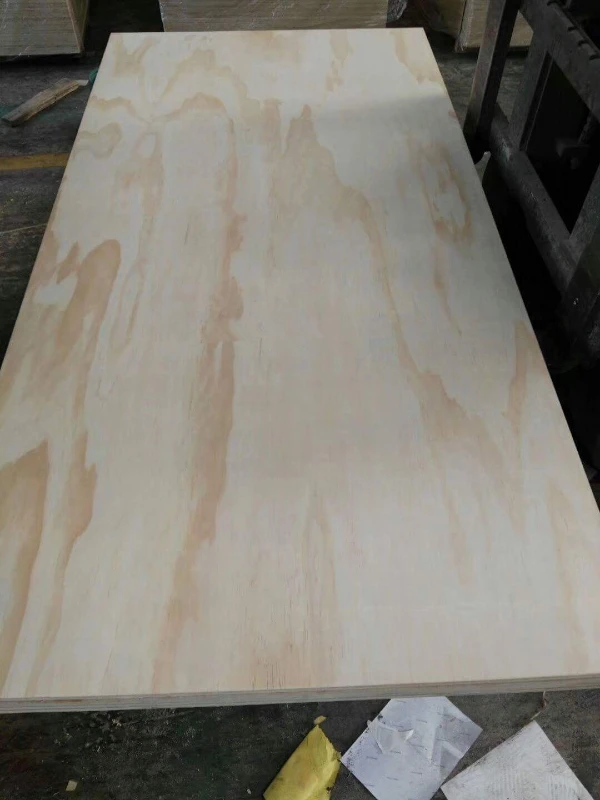
The consistency of plywood is another major advantage. Because plywood is engineered, manufacturers can control its properties, producing panels that meet specific performance quality standards. This reliability is vital in construction projects where structural integrity cannot be compromised. You can generally ensure that a sheet of plywood will perform predictably, unlike solid wood which can have hidden knots or weaknesses. This predictability, combined with its relative affordability and availability in a wide range of sizes and thicknesses, makes plywood an indispensable material for builders, architects, and designers worldwide.
How is High-Quality Plywood Made? Unpacking the Manufacturing Process.
The journey of creating high-quality plywood begins with selecting suitable logs. These logs are often softened by steaming or soaking before being placed on a lathe. The lathe peels the log into long, continuous sheets of wood veneer, much like unrolling a paper towel. These veneers are then dried to a specific moisture content – a critical step to ensure stability and prevent future warping or mold growth. Proper drying is paramount for the longevity and performance of the final plywood panel.
Once dried, the veneers are graded based on their quality and appearance. Defects like knots, splits, or discoloration influence the grade. These graded veneers are then coated with a specialized adhesive. The type of adhesive used is crucial; exterior or structural grades of plywood require waterproof glues (like phenolic formaldehyde resin) to withstand moisture and weather exposure, ensuring durability. The coated veneers are then carefully laid up in layers, remembering the alternating grain direction (cross-graining) that gives plywood its signature strength and stability. The number of plies determines the thickness and strength of the final plywood sheet.
The assembled layers are placed into a powerful hot press. Here, immense heat and pressure are applied, activating the adhesive and bonding the veneers into a single, solid panel. This process creates incredibly strong bonds between the layers. After pressing, the large plywood sheets are trimmed to standard dimensions (like 4x8 feet or specific metric sizes common in markets like Australia), sanded to achieve the desired finish (ranging from rough for sheathing to a smooth finish for cabinetry), and finally graded one last time. Every batch of structural plywood or appearance-grade plywood undergoes rigorous quality checks to ensure it meets relevant standards (e.g., AS/NZS, CARB, CE) before being packaged and shipped. This meticulous manufacturing process ensures that each sheet of plywood delivers reliable performance.
What are the Different Plywood Types Available? From Structural to Specialty.
Plywood isn't a one-size-fits-all product. Different applications demand different properties, leading to a variety of plywood types. Understanding these distinctions is key to selecting the right type for your project. Here's a look at some common categories:
- Structural Plywood: As the name suggests, this type of plywood is designed for strength and load-bearing capacity. It's used in applications like wall sheathing, roof decking, and subflooring where structural integrity is paramount. Structural plywood is graded based on its strength characteristics (e.g., F-grades in Australia like F11 or F17, or performance ratings in North America). The veneers used might not be perfect in appearance, but the adhesive is strong and typically water-resistant. Brands like Rocply structural plywood are engineered to meet specific building code requirements.
- Non-Structural Plywood: This plywood is used where strength is less critical than appearance or basic coverage. Think hoardings, temporary structures, packaging, or internal fixtures. The adhesive might be less water-resistant, and veneer quality varies. It's often a more economical choice for general-purpose use.
- Hardwood Plywood: Made from veneers of hardwood species like oak, birch, or maple. Hardwood plywood is prized for its durability, strength and durability, and attractive grain patterns. It's often used in furniture, cabinetry, architectural millwork, and decorative wall panels where a high-quality finish and aesthetic appeal are desired.
- Softwood Plywood: Constructed from softwood veneers such as pine, fir, or spruce. Softwood plywood is typically used for structural purposes due to its good strength-to-weight ratio and cost-effectiveness. It forms the bulk of plywood used in residential construction for sheathing and subflooring.
- Marine Plywood (Marine-Grade Plywood): This is a high-quality type of plywood specifically engineered for environments with high moisture exposure. Marine plywood is specifically designed using waterproof adhesive (typically WBP - Weather and Boil Proof) and high-quality veneers with minimal core gaps to prevent water trapping. It's essential for boat building, docks, and bathroom or kitchen subflooring in areas prone to moisture. Marine plywood offers superior water resistance and durability.
- Film-Faced Plywood (Formply): This plywood has a resin-impregnated paper film bonded to its surfaces. This film creates a hard, smooth, water-resistant finish, making it ideal for concrete formwork – the film prevents concrete from sticking and allows the panels to be reused multiple times. Formply F17 2400x1200x17mm is a common specification in construction, known for its durability and predictable performance.
Choosing the correct type of plywood ensures your project not only looks good but performs safely and lasts for years. You need to ensure the selected plywood matches the demands of the application.
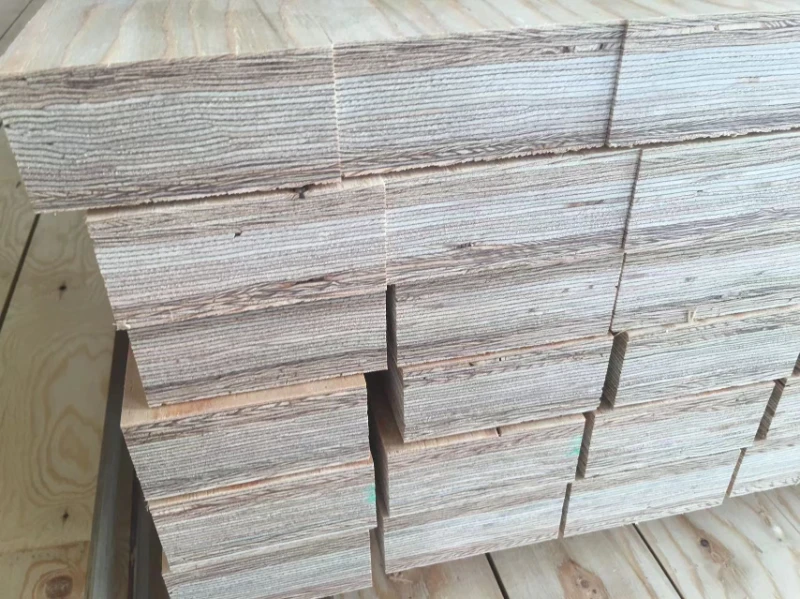
Why is Structural Plywood Essential for Load-Bearing Applications?
When building structures designed to support weight – whether it's a roof holding up snow, a floor supporting furniture and people, or walls resisting wind forces – you absolutely need materials you can trust. This is where structural plywood shines. Plywood is engineered specifically to provide predictable strength and durability under load. The cross-laminated construction of structural plywood is key; it distributes stress across the entire panel, resisting forces that could cause solid wood to split or break along the grain. This inherent stability is crucial for maintaining the structural integrity of a building over its lifetime.
Structural plywood undergoes rigorous testing and grading to ensure it meets specific performance benchmarks outlined in building codes and standards (like AS/NZS 4357 in Australia or PS 1 and PS 2 standards in the USA). These grades (e.g., F8, F11, F17, F22) directly relate to the plywood's bending strength, stiffness, and shear resistance. Architects and engineers rely on these ratings to specify the correct plywood thickness and grade for different load-bearing elements like beams, floor joists (often in conjunction with materials like I-Joist/Floor Joist), wall sheathing, and roof decking. Using plywood not rated for structural purposes in these critical areas can lead to structural failure, posing significant safety risks.
Furthermore, the manufacturing controls for structural plywood ensure consistency. Unlike natural timber, which can have unpredictable variations in density and defects, structural plywood provides a uniform material property across the sheet and from sheet to sheet within the same grade. This reliability simplifies structural design and construction, ensuring the building performs as intended. The use of durable, often waterproof adhesive in structural plywood also contributes to its longevity, helping it withstand incidental moisture exposure during construction and throughout the building's service life. For any application where safety and load-bearing capacity are non-negotiable, structural plywood is not just a good choice; it's often the required one.
How Does Plywood Compare to Solid Wood or Other Panels like OSB?
Choosing the right panel product involves understanding the strengths and weaknesses of each option. Plywood, solid wood, and Oriented Strand Board (OSB) are common choices, each with distinct characteristics:
Plywood vs. Solid Wood:
- Stability: Plywood is significantly more dimensionally stable than solid wood. Due to its cross-grained structure, it resists shrinking, swelling, warping, and twisting much better, especially with changes in humidity. Solid wood moves more across the grain.
- Strength: Plywood offers high uniform strength across the panel. While solid wood can be very strong along the grain, it's weaker across the grain and prone to splitting. Plywood's strength-to-weight ratio is generally excellent.
- Consistency: Plywood is engineered for consistency. Solid wood has natural variations like knots and grain patterns that can affect its strength and appearance.
- Cost & Sizes: Plywood is often more cost-effective than high-quality solid wood of similar dimensions and is readily available in large, standard sheet sizes (e.g., 4'x8'). Solid wood availability in large, clear pieces can be limited and expensive.
- Appearance: High-grade hardwood plywood can offer a beautiful wood finish, but some prefer the unique character and potential for intricate carving found only in solid wood.
Plywood vs. OSB:
- Composition: Plywood is made from thin layers of wood veneer. OSB is made from compressed wood strands or flakes arranged in layers (oriented) and bonded with adhesive.
- Strength & Stiffness: Structural plywood and structural OSB can have similar strength ratings, but plywood is generally considered stiffer. Plywood also tends to hold nails and screws better near the edges without splitting.
- Moisture Resistance: Standard plywood and OSB have similar reactions to incidental water. However, when exposed to prolonged moisture, OSB edges can swell more significantly and permanently than plywood. Marine-grade plywood offers superior water resistance compared to any standard OSB.
- Consistency: Both are engineered panels offering good consistency, though OSB can sometimes have minor variations in density or surface texture.
- Cost: OSB is typically less expensive than plywood of a comparable thickness and structural rating, making it a popular choice for sheathing and subflooring where cost is a major driver.
- Appearance: Plywood generally has a smoother surface and more traditional wood grain appearance (especially hardwood plywood) than OSB, which has a visible strand pattern.
Table: Plywood vs. OSB vs. Solid Wood (General Comparison)
Feature | Plywood | OSB (Oriented Strand Board) | Solid Wood |
---|---|---|---|
Stability | Very High (Cross-grained) | High | Moderate (Moves with humidity) |
Strength | High, Uniform | High, Uniform | High along grain, weaker across |
Stiffness | Generally Higher than OSB | Good | Variable |
Moisture | Good (Exterior/Marine grades excellent) | Good (Edges prone to swelling) | Variable (Depends on species/finish) |
Consistency | Very High | High | Variable (Natural defects) |
Cost | Moderate | Lower than Plywood | Higher (Especially clear grades) |
Appearance | Wood Veneer (Smooth/Grained) | Visible Strands | Natural Grain/Character |
Sizes | Large Sheets Standard | Large Sheets Standard | Limited by Log Size |
Ultimately, the best choice depends on the specific application, budget, and required performance characteristics. Plywood offers a balanced blend of strength, stability, and versatility, making it suitable for a huge range of uses.
What Should Buyers Look for When Sourcing High-Quality Plywood Overseas?
Sourcing building materials like plywood internationally, particularly from countries like China or Vietnam, presents great opportunities for cost savings but also requires diligence to ensure quality and reliability. For buyers like Mark Thompson, who prioritize quality alongside competitive pricing, several factors are critical:
-
Verified Certifications: Don't just take a supplier's word for it. Request copies of certifications relevant to your market and application. This could include:
- Structural Ratings: AS/NZS standards (e.g., AS/NZS 2269 for Structural Plywood) if exporting to Australia/New Zealand, or PS 1/PS 2 for North America.
- Adhesive Quality: Look for stamps indicating bond type (e.g., WBP, Type A Bond) for exterior or structural plywood.
- Formaldehyde Emissions: CARB Phase 2 or EPA TSCA Title VI (for USA), E0/E1 (Europe/Asia) are crucial for indoor air quality, especially for plywood used in furniture or interiors.
- Sustainability: FSC (Forest Stewardship Council) or PEFC certification if environmentally sourced plywood is required.
- Action: Ask for certificate numbers and verify them through the issuing body's database if possible. Be wary of falsified documents – a common pain point.
-
Detailed Specifications & Grade Confirmation: Clearly define the required plywood specifications: thickness, dimensions, wood species (face/back/core), grade (e.g., B/C grade, CDX, specific F-grade), adhesive type, and any special requirements (e.g., specific finish, edge sealing).
- Action: Get written confirmation that the supplier understands and agrees to meet all specifications for every batch of structural plywood or other plywood ordered. Request specification sheets.
-
Quality Inspection Procedures: Understand the factory's internal quality control (QC) processes. More importantly, consider arranging independent third-party inspections.
- Key Checks: Dimensional accuracy (thickness, squareness), moisture content (critical to prevent warping/mold), lamination quality (check for delamination or core gaps/voids), face/back veneer quality (matching the agreed grade), and packaging quality.
- Action: Specify acceptable tolerances for dimensions and moisture content in your purchase order. Discuss how defects are handled. Third-party inspection before shipment provides unbiased verification. As a factory (Jsylvl), we welcome customer or third-party inspections as it builds trust.
-
Supplier Reputation and Experience: Look for established suppliers with a track record of exporting to your country or region.
- Finding Suppliers: Exhibitions (like Canton Fair, IBS, BAU) are good for initial contact, as is targeted Google searching. Look for suppliers specializing in the type of plywood you need (e.g., structural plywood, formply).
- Action: Ask for references from buyers in your market. Check online reviews or industry directories. A supplier accustomed to your market's standards is less likely to cause issues.
-
Clear Communication & Logistics: Ensure clear communication regarding production lead times, shipping terms (FOB, CIF), payment methods, and documentation requirements for customs clearance.
- Action: Maintain open communication channels. Confirm shipping schedules regularly. Delays can severely impact construction timelines – a major pain point for buyers. We strive to deliver plywood reliably and on schedule.
By focusing on these areas, buyers can significantly mitigate risks associated with overseas sourcing and build strong relationships with reliable suppliers like us at Jsylvl, ensuring they receive high-quality plywood that meets their project needs and quality standards.
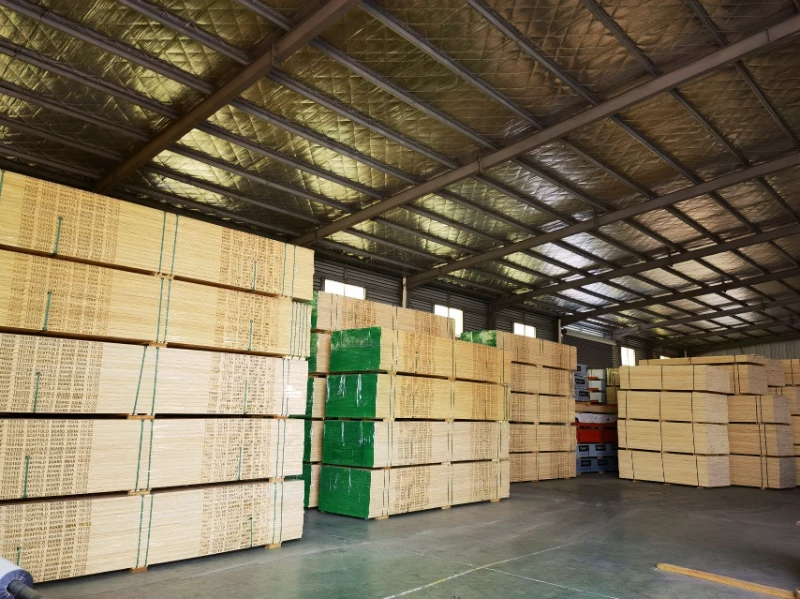
Can Plywood Be Used for More Than Just Structural Applications? Exploring Versatility.
Absolutely! While structural plywood forms the hidden backbone of many buildings, the versatility of plywood extends far beyond load-bearing roles. Its unique combination of workability, stability, and potential for beautiful finishes makes it suitable for a vast array of non-structural and decorative uses. Plywood is commonly used in applications where aesthetics, form, or specific functions other than pure strength are primary.
In furniture making, hardwood plywood is a star. It provides large, stable panels with attractive wood grain faces (like oak, birch, walnut) perfect for tabletops, cabinet carcasses, drawer sides, and shelving. Using plywood avoids the expansion/contraction issues of wide solid wood panels and is often more economical than equivalent-sized solid wood. The layered edges of plywood can even be left exposed and finished for a modern, distinctive look. Similarly, plywood is a favorite for architectural millwork, wall paneling, and creating curved forms, as thinner sheets can be bent more easily than solid wood.
Plywood is also a staple for DIY enthusiasts and hobbyists. Its ease of cutting, shaping, and joining makes it accessible for projects ranging from simple storage boxes and workshop jigs to intricate crafts and model making. Non-structural plywood grades offer an affordable material for practice or projects where appearance is less critical. Specialty plywood types, like flexible plywood (designed to bend easily) or plywood with decorative overlays, further expand the creative possibilities. From skateboards to speaker boxes, stage sets to signage, plywood provides the flexibility and reliability needed for countless creative and functional applications beyond basic construction. Its adaptability truly makes it suitable for nearly any wood-based project imaginable.
What are the Key Benefits of Using Plywood in Construction and Design?
The enduring popularity of plywood in construction and design isn't accidental. It stems from a combination of practical advantages that make it a reliable and efficient material choice:
- High Strength-to-Weight Ratio: Plywood packs impressive strength into a relatively lightweight panel. This makes structures built with plywood strong without being excessively heavy, which can simplify foundation requirements and make handling on site easier.
- Dimensional Stability: Thanks to its cross-laminated structure, plywood resists shrinking, swelling, warping, and twisting far better than solid wood. This stability is crucial for maintaining tight fits and finishes over time, especially in fluctuating humidity.
- High Impact Resistance: The layered construction distributes the force of impacts, making plywood very durable and resistant to shattering or puncturing compared to some other panel types. This adds to the overall durability of the assembly.
- Panel Shear Strength: Plywood excels in resisting racking forces (forces that try to push a square frame out of shape). This makes it excellent for wall sheathing and roof diaphragms, contributing significantly to a building's overall rigidity and resistance to wind or seismic loads. Structural plywood is specifically rated for this.
- Design Flexibility & Versatility: Plywood can be easily cut, drilled, shaped, and fastened using standard woodworking tools. It comes in various thicknesses, grades, and species (including hardwood plywood for appearance). It can be used for structural frames, subfloors, sheathing, cabinetry, furniture, formwork (film faced plywood), and more. This versatility is unmatched.
- Surface Finish Options: Plywood can be manufactured with surfaces ready for painting, staining, laminating, or veneering. Higher grades offer a smooth finish suitable for visible applications, while structural plywood provides a sound base for the final finish.
- Cost-Effectiveness: While initial cost varies by grade and type, plywood often provides excellent value considering its strength, stability, and large panel size, which can reduce labor time compared to installing individual boards. Non-structural plywood options offer economical solutions for general purposes.
- Sustainability: Plywood makes efficient use of timber resources, often utilizing logs not suitable for solid wood lumber. Look for plywood sourced from sustainably managed forests (e.g., FSC or PEFC certified) to ensure environmental responsibility.
These combined benefits ensure that plywood remains a go-to material for architects, engineers, builders, and designers seeking performance, reliability, and value in their projects.
How Do You Choose the Right Plywood Solution for Your Project? A Practical Guide.
Selecting the right plywood involves matching the material's properties to the demands of the job. Making the wrong choice can lead to subpar performance, reduced longevity, or even structural issues. Here’s a practical approach to finding the perfect plywood:
-
Identify the Application: What will the plywood be used for?
- Structural: Wall sheathing, roof decking, subflooring, beams? You need structural plywood meeting specific load requirements (e.g., F-grade, PS-rated).
- Exterior: Exposed to weather or high moisture (docks, boat parts, some siding)? Marine-grade plywood or properly rated exterior plywood with waterproof adhesive is essential.
- Interior - Functional: Cabinet carcasses, shelving, underlayment? Hardwood plywood (for appearance/durability) or a stable sanded plywood might work.
- Interior - Decorative: Furniture, visible wall panels, architectural features? Hardwood plywood with a specific veneer grade (A or B) for a clean finish is likely needed.
- Concrete Formwork: Use Film-Faced Plywood (Formply) designed for smooth release and multiple reuses.
- General Purpose / DIY Projects: Non-structural plywood or utility grades might suffice if high strength or perfect appearance isn't critical.
-
Determine Required Strength & Grade: If it's structural, consult building plans or codes for the necessary grade (e.g., F11 structural plywood, CDX sheathing). For non-structural uses, consider the needed stiffness and durability. Plywood is graded based on veneer quality (A, B, C, D - A being best, free of visible defects) and structural performance.
-
Consider Exposure & Environment: Will the plywood get wet or experience high humidity? This dictates the required adhesive type (interior, exterior WBP) and potentially the need for marine plywood. Standard interior plywood will delaminate if exposed to moisture. Ensure you choose adequate water resistance.
-
Select Thickness: Thicker plywood is generally stronger and stiffer but also heavier and more expensive. The application dictates the appropriate thickness (e.g., 3/4" for subflooring, 1/2" for wall sheathing, 1/4" for cabinet backs).
-
Evaluate Finish Requirements: Do you need a perfectly smooth surface for painting or clear coating (hardwood plywood A/B grades)? Or is a rougher surface acceptable (C/D grades for sheathing)? Sanded plywood provides a better finish than unsanded.
-
Check Certifications: Ensure the plywood carries the necessary certifications for your region and application (structural ratings, emissions standards like CARB/E0, sustainability like FSC).
-
Factor in Budget: Higher grades, specialty types (marine plywood, hardwood plywood), and thicker panels cost more. Balance performance needs with budget constraints. Sometimes a lower grade (non-structural plywood) is perfectly adequate and saves money.
By carefully considering these factors, you can confidently select the right type of plywood for your project, ensuring it performs correctly, looks appropriate, and provides long-lasting value. Consulting with a knowledgeable supplier like Jsylvl can also help you navigate the options and find the perfect fit.

What Future Trends are Shaping the Rocply Structural Plywood Industry?
The plywood industry, including specialized products like Rocply structural plywood, is constantly evolving to meet new demands in construction and design, driven by factors like sustainability, efficiency, and technological advancements. We see several key trends shaping the future:
- Enhanced Sustainability: Growing environmental awareness is pushing demand for plywood sourced from certified, sustainably managed forests (FSC/PEFC). Manufacturers are also exploring greener adhesive technologies with lower volatile organic compound (VOC) emissions and formaldehyde-free options, responding to stricter indoor air quality regulations (like CARB and E0 standards). Efficient resource utilization during the manufacturing process is also a focus.
- Performance Optimization: There's ongoing research into enhancing plywood properties. This includes developing panels with even higher strength-to-weight ratios, improved fire resistance, and greater durability against moisture and pests. Engineered plywood variants might incorporate composite materials or specialized treatments to meet niche performance requirements.
- Digital Integration & Precision Manufacturing: Advanced manufacturing techniques allow for greater precision in veneer peeling, drying, and pressing. This leads to more consistent plywood quality and potentially customized panel sizes or shapes directly from the factory, reducing on-site waste. Digital tools are also improving traceability and quality control throughout the supply chain.
- Competition & Hybrid Solutions: Plywood faces ongoing competition from other panel products like OSB and newer composite materials. This spurs innovation in plywood itself but also leads to hybrid solutions, such as I-Joists using plywood or LVL flanges with OSB webs (I-Joist/Floor Joist are a prime example), combining the best properties of different materials for optimal performance and cost-effectiveness.
- Focus on Resilience: With increasing concerns about extreme weather events, there's a growing demand for building materials that contribute to resilient construction. The inherent strength and diaphragm action of structural plywood play a vital role in creating buildings better able to withstand high winds and seismic activity. Future developments may further enhance these properties.
As a manufacturer (Jsylvl), staying ahead of these trends is crucial. We continuously invest in technology and sustainable practices to ensure our plywood products, including structural plywood and other engineered wood solutions, meet the evolving needs of the global construction market, delivering both performance and environmental responsibility. The future of plywood lies in being stronger, smarter, and greener.
Key Takeaways on Plywood:
- Plywood is Engineered Strength: Its cross-laminated veneer construction provides exceptional stability, strength-to-weight ratio, and resistance to splitting compared to solid wood.
- Versatility is King: From heavy-duty structural plywood in framing to beautiful hardwood plywood in furniture and rugged marine plywood for wet areas, there's a type of plywood for almost any application.
- Grade Matters: Plywood is graded based on veneer quality and structural performance. Ensure you choose the right grade (e.g., structural, non-structural, A/B/C/D faces) and adhesive type for your project's needs and exposure conditions.
- Manufacturing Precision: High-quality plywood relies on careful veneer selection, controlled drying, appropriate adhesive application, and precise pressing to ensure consistent performance and durability.
- Sourcing Requires Diligence: When buying plywood, especially overseas, verify certifications (structural, emissions, sustainability), confirm detailed specifications, understand QC processes, and choose reputable suppliers to avoid common pain points like inconsistent quality or delays.
- Beyond Structure: Don't underestimate plywood’s versatility for non-structural uses like cabinetry, DIY projects, decorative panels, and formwork (film faced plywood).
- Informed Selection is Crucial: Choosing the right plywood for your project ensures safety, longevity, proper function, and aesthetic appeal. Consider application, strength needs, environment, thickness, and finish.
- Future is Evolving: The plywood industry is advancing with trends towards greater sustainability, enhanced performance, and digital manufacturing integration.
Understanding these points empowers you to leverage the many benefits of plywood, the true workhorse and backbone of modern construction and design.
Post time: Apr-11-2025